Aviation Oil Analysis
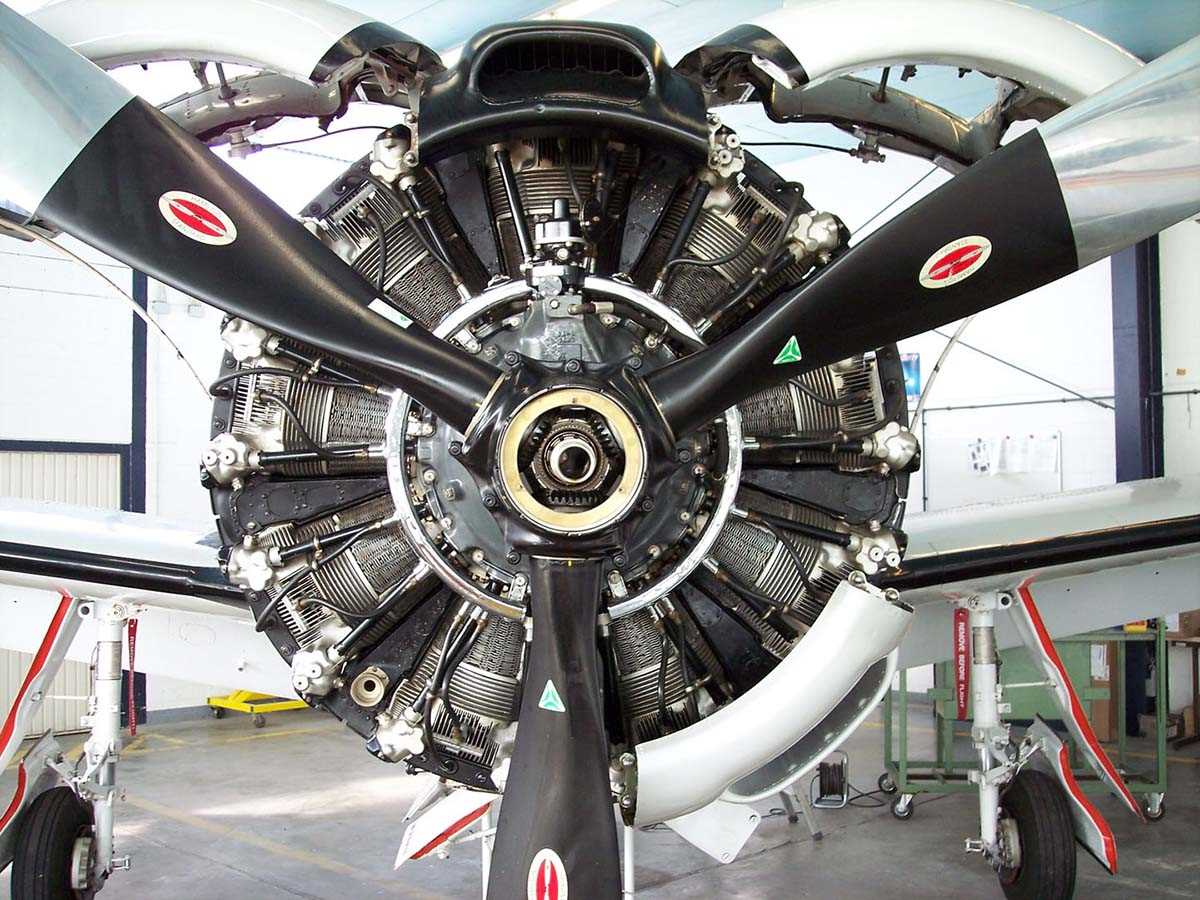
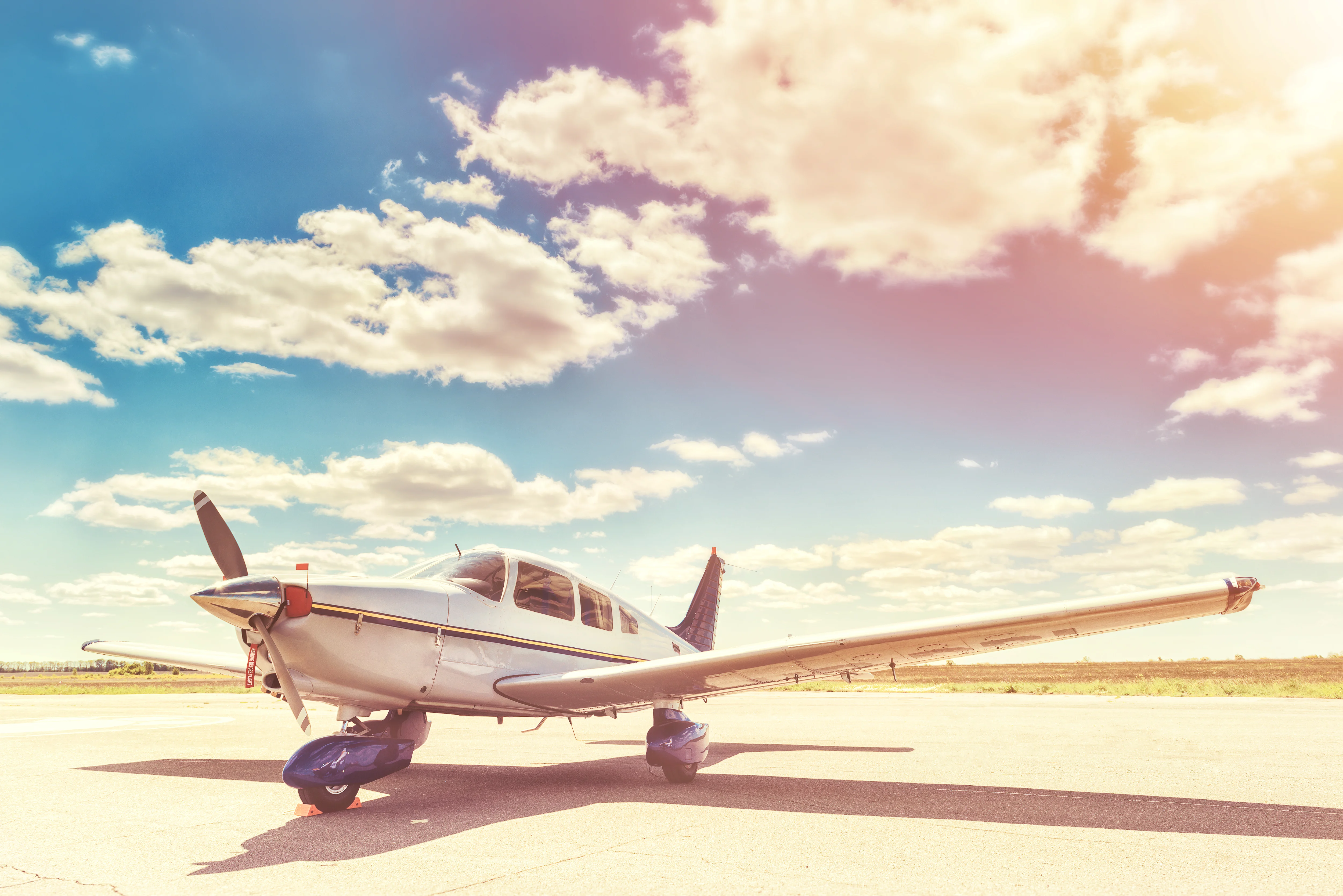
Oil analysis is useful in keeping you informed on the internal conditions of your equipment. It is an essential maintenance tool that helps you predict potential failure and adverse wear trends to ensure safe and successful operations whether you fly a few hours every year or hundreds of hours.
What is Aviation Oil analysis?
It is the routine study of aircraft oil to monitor wear levels and fluid conditions. The wear particles comes from two or more moving parts that touch. Proper lubrication can reduce the amount of friction between the moving parts, but microscopic pieces of metal are still generated during engine start up, from dirt, contamination, corrosion and poor lubrication. A sample of the oil can be analyzed to assess potential problems and notify the owner or mechanic to wear, contamination and the characteristic of the lubricant.
Aviation oil analysis is beneficial, as routine sampling can reduce downtime by allowing for scheduled maintenance and repairs, lower the cost by determining the proper repair window. Analyzing too frequent and you are spending money on items not needed, too late and your repair could be more costly than if action was taken sooner.
How often should I test my oil?
For aircraft it is recommended you test every time you change the oil which is typically 25-50 hours. A consistent routine should be implemented, if you decide to sample at “x” hours you should continue to do so roughly every “x” hours. Routine sampling has the benefit of trend analysis. Trending allows you to see how your engine functions over time and allows you to look back on the history of your engine.
What testing is performed?
One of the key tests is Inductively Coupled Plasma Emissions Spectroscopy, also known as ICP. The ICP uses a plasma heat source to excite the electrons of the particles in the oil. Once excited they give off photon (radiated light) emissions which are then captured by the ICP to measure metal concentration by parts per million detected.
These concentrations of metals can be used to determine the source of wear or contamination. For example, high concentrations of Aluminum can indicate issues with the pistons, oil pump, accessory cases, turbo or washers. High Aluminum and Iron can also be present due to corrosion after extended down time of an engine.
Other beneficial testing includes Viscosity, Particle Quantification Index (PQI), Microscopic Particle Examination (MPE) and inspection of the filter.
Viscosity is the measure of an oil resistance to flow; in basic terms how thick the oil is.
PQI helps to monitor the ferrous debris in system, some ferrous debris is large than 20 microns and is more easily detected by a ferrous debris monitor than the ICP which is optimized to detect metals on a more microscopic level.
MPE helps determine the metal constituents and the type of wear such as Ferrous and nonferrous wear particles, cutting wear, corrosive wear, oxides from excessive heat and friction polymer from excessive load.
An inspection of the filter pleats checks for abnormal amounts of metal chips and the size of the largest particle present.
After all the testing is completed a diagnostician will evaluate the results of the test and provide observations and recommendations in a report. If a sample of the engine oil has previously been evaluated those result will show up on the report allowing for easy review of historical samples and trends.
Aviation oil analysis is an important part of owning and operating a plane. Not only does it help your engine run better and last longer but ensures the safety of the pilots and their passengers. For more information please contact ALS Tribology laboratory or any of our regional testing labs to meet your aviation oil analysis needs.
Written By:
Madison Dawn
Laboratory Manager, Phoenix
ALS Tribology