Transformer Oil Analysis to increase asset life
Condition monitoring in 2022 includes many different methods, but oil analysis remains one of the most cost effective ways to extend asset life.
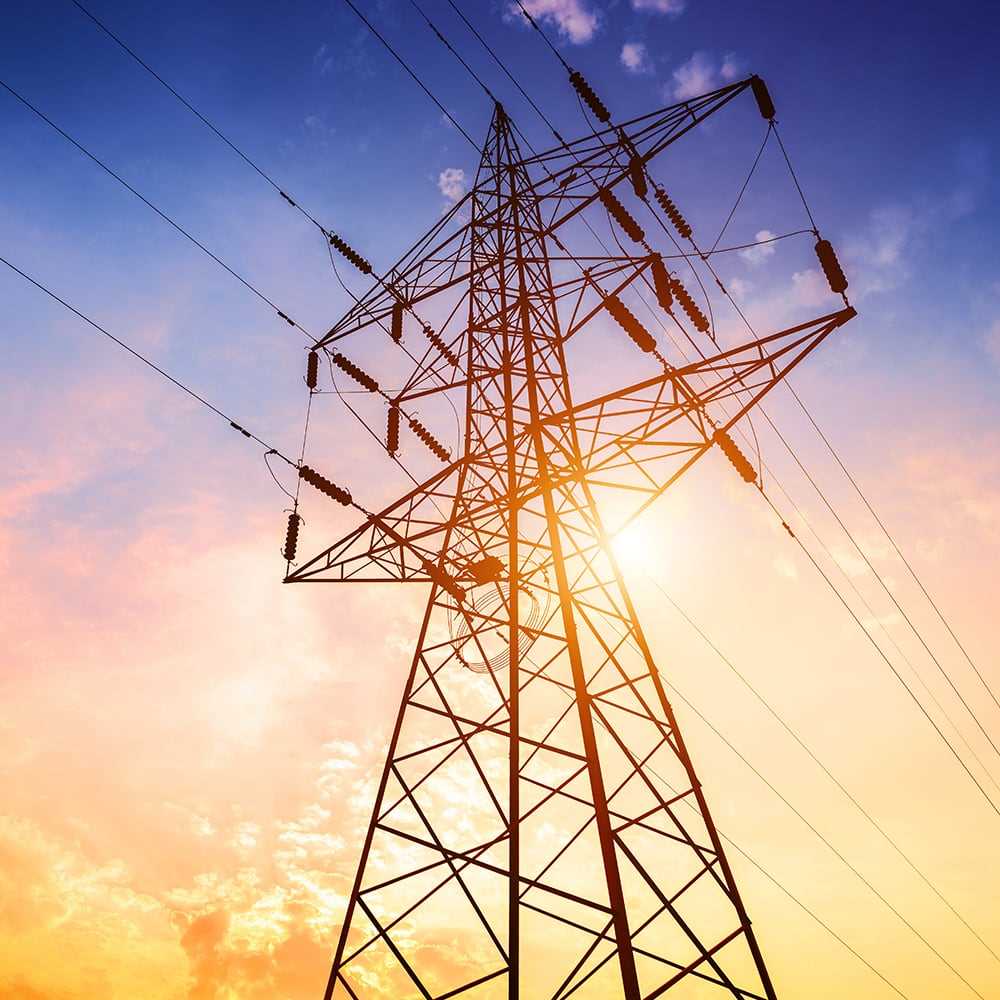
Condition monitoring, including oil analysis, is the frequent collecting, measuring, and analysis of relevant data. With the right partner to assist in interpreting the data correctly, it can provide you valuable insight on the condition of your asset. Allowing you to take ownership on how to react and maintain that asset.
For transformers that can be around for 50 years or more if properly maintained it could mean a lot of savings for many years. The cost of an oil analysis will cost $225, usually taken once a year and for that cost you receive valuable insight on how the transformer is performing and what actions your maintenance team may need to take.
But there are some secrets to optimizing your oil analysis program:
Set up is one of the most important aspects of a well-run oil analysis program. It is important to identify the key parameters that you need to get a full picture of the status of the transformer and the actions needed for ongoing reliability of the transformer which will support the life expectance of the transformers.
Data Insights
- Have there been any changes in the condition of the transformer since the last oil analysis or maintenance activity?
- Is the trending data show any degradation that is occurring?
- Is the oil performing as it should to support its function as an insulator?
- Are any repetitive issues arising that should be a concern?
- The assets estimated longevity and what may impact that?
- Should an action be taken before the next scheduled maintenance activity?
How can Oil Analysis be a Cost Savings?
Predictive maintenance practices, when done properly, are known to be effective way program to save money. However, like anything great if implemented the wrong way it will not give you the value you want.
Information is the key along with interpretation. The more accurate the information you have will allow for far better interpretation of the data. The most effective programs include proper sampling, testing and analysis of in-service lubricants. When done properly and over time, the condition of your asset can be trended to give you the red flags you need.
Those red flags, or insights coming from the oil analysis in return help you to predict the life expectancy of that equipment and also help to effectively schedule the appropriate maintenance actions to be taken to help protect your asset.
A failure of a large power transformer could cost millions in lost revenue because of how long it may take to replace, repair, etc. Even worse a failed transformer could cause a fire and explosion, putting lives at risk.
A typical service call for a (transformer) could cost $500 and a simple part fix will cost $1000. While annual oil analysis will run you $225. By saving one minor emergency service call for a minor fix will pay for the cost of your program while giving you additional benefits of helping you prevent expensive overhaul/replacement costs, maximizing lubricant life, and minimizing or completely avoiding unexpected downtime or even catastrophic failure.
Contact an ALS representative today to learn how Transformer Oil Analysis can help your maintenance program save money.