Compatibility of Lubricant Mixtures
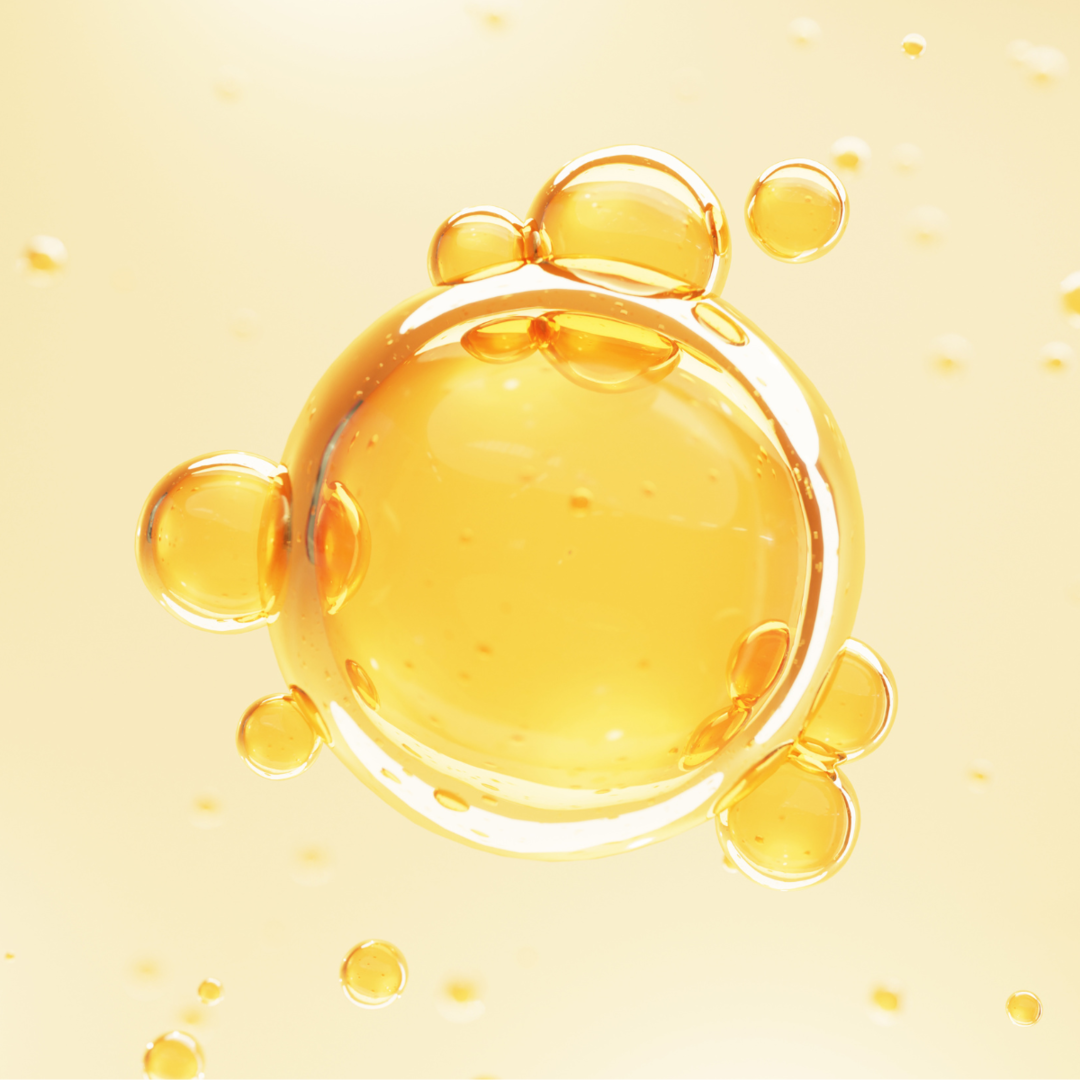
Mixing of two incompatible lubricants can compromise the overall performance of the combined products in service. This can result in a fluid which is inferior to the quality of the original products before they were combined.
As product formulations in industrial oil applications become more complex, lubricant compatibility can be a concern. Mixing of incompatible lubricants in a circulating system can lead to the formation of insoluble materials plugging flow passageways, additive dropout, and reservoir sludge build up. Mixing of two incompatible lubricants can compromise the overall performance of the combined products in service. This can result in a fluid which is inferior to the original products before they were combined.
The most common problem occurs when a lubricant which has an acidic additive package is combined with a lubricant using an alkaline-based additive package. This acid-based mixture will result in insoluble soap materials being created, which can cause filter and passageway plugging. Most lubricant additives exist in balanced concentrations. Lubricants with dissimilar additive chemistry can reduce the overall effectiveness of the additives or cause them to fall out of solution. Component materials such as seals can also be negatively affected.
PQ Index data can also help determine overall size concentration of iron particles. Low iron test results and a high PQI would indicate overall particles are large (>20 micron). High iron test results and a low PQI would indicate overall particles are small (<10 micron). If iron and PQI results are at relatively the same concentration, then it usually indicates overall size range of the particles is small. Seeing a test report with low iron test results and a high PQI, indicating overall large particles, can also predict accelerated wear or impending catastrophic wear, especially if there is a sudden upswing in the trend analysis.
One of the challenges today is the mixing of lubricants formulated with group I base oils with products formulated with group II and group III base oils, or mineral oils with certain synthetic-based products. Many additives that can remain in suspension in group I base oils do not work as well in group II or III base oils. Also, the type of additives that perform a particular function in a group I base oil may have different chemistry in group II or III base oil for the same function. Certain synthetic lubricants cannot be mixed with mineral oilbased products. Many products simply do not blend and separate when given the chance, especially in the reservoir. Seal degradation, bearing and pump failures can result from these mixtures.
When changing from one lubricant product to another in an industrial application, it is recommended that endusers consult their lubricant supplier for guidance. Not all lubricants may be incompatible simply because they are from a different supplier. Oils with similar chemistry would not cause a concern. As an example, many AW Hydraulic oils are similar in chemistry and would not cause a problem if mixed. Lubricants with dissimilar chemistry in either the additive packages or base oil formulations are the concern.
Products can be tested for compatibility by a laboratory. Test Method ASTM D7155 provides a standard practice for evaluating the mixture of two lubricants for compatibility. Generally, two products are mixed at varying concentrations and observed for clarity and the formation of precipitates and sediment. The observations are conducted at varying temperatures for established lengths of time. Combined product performance can be looked at by employing additional subsequent testing for foaming, rust prevention, corrosion, water separability, and other types of tests.
Always consult with your lubricant supplier when changing to a different product in your lubrication circulating system. If still in doubt, request additional testing of the mixture before combining products. Even an on-site visual observation with a simple mixture may show signs of incompatibility after setting for a few days to a week. If you require any assistance with instructions on taking your sample or understanding the analysis report that you receive from ALS, please contact us via email: reliability@alsglobal.com.