¿Cómo calcular la disponibilidad de una máquina?
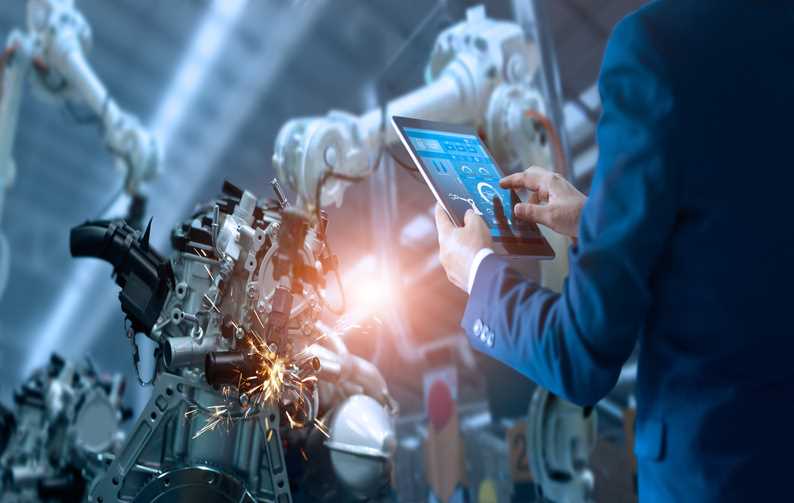
Por lo tanto, es posible definir listas de prioridad, atención e historial de las máquinas, también rastreando su disponibilidad y confiabilidad y siempre buscando aumentar el índice de disponibilidad. Esta acción también aumenta la productividad y, si está bien implementada, reduce los costos de mantenimiento.
Calcular la disponibilidad de una máquina
Sin embargo, ¿cómo calcular la disponibilidad de una máquina? Hay varios puntos de partida para este cálculo, ya que existen, de manera similar, diferentes posibilidades para medir el tiempo del sistema parado y en funcionamiento.Algunos cálculos son los de disponibilidad instantánea, disponibilidad promedio, disponibilidad constante del estado (asintótica) o incluso por métodos de cálculo característicos de cada empresa, con la disponibilidad operativa e inherente. Hablemos de esto último, comúnmente aplicado en empresas:
Disponibilidad inherente
Es la disponibilidad de un estado estable, considerando solo el tiempo de inactividad del equipo, debido a paradas para un mantenimiento correctivo. En otras palabras, la interrupción debido al mantenimiento preventivo, detalles logísticos y demoras en el suministro, se excluyen, ya que se consideran ideales, y solo evalúan el tiempo debido a la inactividad, utilizado para acciones de mantenimiento correctivo.
El cálculo de disponibilidad se realiza de acuerdo con los siguientes criterios:
¿Qué es MTBF y MTTR?
MTBF significa «Mean Time Between Failures«, que significa tiempo medio entre fallas, y MTTR significa «Mean Time To Repair «, es decir, el tiempo medio para reparar.Estos datos sirven para medir la confiabilidad de los equipos. Ambos índices se utilizan como punto de referencia para la toma de decisiones en las empresas.
El objetivo siempre es aumentar el MTBF y disminuir el MTTR.
Cómo medir MTBF
Esta métrica se refiere al tiempo promedio transcurrido entre una falla y la siguiente. Estas fallas deben estar relacionadas con factores de mantenimiento directo. Los factores externos que afectan la producción, no se consideran defectos en este cálculo.Usaremos el tiempo de operación normal total durante un período predeterminado, en la cantidad de fallas que ocurrieron durante ese período.
MTBF = (Tiempo total que la máquina está disponible para funcionar) / (Total de paradas)
Ejemplo:
Durante un cierto período de tiempo para operar se observó:
Tiempo total disponible para operar = 24 horas
Hubo 3 paradas debido a problemas con las máquinas, cada una de las cuales fue: 1 hora, 2 horas y 30 minutos (0,5 horas).
MTBF = [24 – (1 + 2 + 0.5)] / 3 = 6.83 horas o 410 minutos
Al estudiar las fallas y conocer el tiempo entre ellas, pudimos diseñar estrategias para mitigar, o incluso resolver un problema del equipo.
Cuanto mayor sea el MTBF, menor será el número de paradas para este equipo.
Cómo medir MTTR
El MTTR se calcula utilizando el tiempo promedio que lleva realizar una reparación después de que se haya producido la falla.MTTR = (Tiempo total de reparación) / (número de fallas)
Pensemos en el mismo ejemplo anterior. Llegamos al siguiente resultado:
MTTR = (1 + 2 + 0.5) / 3 = 1.16 horas o 70 minutos
Este resultado indica el tiempo promedio que la máquina estuvo parada.
Cuanto más bajo es el MTTR, más eficiente es el equipo de mantenimiento.
Beneficios de usar MTTR y MTBF
Con estos, podemos ampliar el conocimiento de la empresa sobre sus procesos. Esto es especialmente útil para los equipos de mantenimiento que están compuestos por empleados que se dedican a varias áreas al mismo tiempo.Después de establecer una frecuencia optimizada para monitorear los dos indicadores, comience a implementar los siguientes pasos:- Identificación de fallas: con el informe en la mano, puede observar ocurrencias por tipo de falla y el impacto en el tiempo de inactividad de estas ocurrencias. De esta manera, puede ajustar el tipo de problema e identificar si se trata de un componente específico que puede tener un problema.
- Reducción del tiempo de inactividad: ahora sabe cuál componente causa la mayoría de los problemas y, de esta manera, puede arreglarlo.
- Diseñar un proceso de mantenimiento predictivo. No cometa el error de realizar siempre el mantenimiento correctivo sin intentar comprender la raíz del problema.
Otro indicador que utiliza el concepto de disponibilidad es el OEE.
OEE
OEE significa «Efectividad General del Equipo» (Overall Equipment Effectiveness) y es el principal indicador de la efectividad global de una máquina, siendo ampliamente utilizado en las industrias manufactureras. Con este, es posible verificar el uso de los recursos disponibles por la empresa (máquinas, mano de obra y materiales), desmembrando la eficiencia en sus 3 indicadores.
DÓNDE:
Disponibilidad
Es el porcentaje del tiempo que el equipo estuvo funcionando, comparado con el tiempo total disponible para su uso.
Cálculo: Disponibilidad % = (Tiempo de producción / Tiempo programado para producir) * 100
Rendimiento
Relación entre la capacidad real con la capacidad nominal -o deseada- del equipo (importante tener en cuenta que no siempre operamos con la capacidad nominal real del equipo, sino con la capacidad de producción esperada, que debe estar dentro de la capacidad nominal de la máquina).
El tiempo en que la máquina estuvo funcionando por debajo de la capacidad adecuada indica una pérdida de rendimiento, que puede deberse a paradas operativas cortas, o debido a fallas que son inherentes al mantenimiento.
Cálculo: Rendimiento % = (Cantidad de producción real / Cantidad de producción programada) x 100
Calidad
Relación entre el total de las partes conformes y el total de las partes producidas (incluidas las partes no conformes, es decir, que tuvieron que ser reelaboradas o desechadas).
Cálculo: Calidad % = (Cantidad de artículos conformes / Cantidad total producida) x 100
Cálculo de OEE
Dado que los factores de disponibilidad, rendimiento y calidad están disponibles para calcular el OEE, simplemente haga el producto entre ellos:
OEE = Disponibilidad % * Rendimiento % * Calidad %
La siguiente tabla, de www.oee.com, ayuda a comprender:
PÉRDIDA | FACTOR OEE
Pérdida del Horario
◘ No forma parte del cálculo OEE.
Pérdida de la Disponibilidad
◘ La Disponibilidad es la proporción entre el Tiempo de Operación en la Planificación de Producción.
◘ Se toman en cuenta las Fallas del Equipo (paradas inesperadas) y la Configuración y Ajustes (paradas previstas).
◘ La Disponibilidad en 100% implica que el proceso en la Planificación de Producción no presenta Tiempos de Parada.
Pérdida del Rendimiento
◘ El Rendimiento es la proporción del Tiempo de Operación.
◘ Considera el Ocio, las Paradas Cortas y la Velocidad Reducida.
◘ El Rendimiento en 100% implica que el proceso de manufactura está a máxima velocidad.
Pérdida de la Calidad
◘ La Calidad es la proporción del Tiempo de Producción.
◘ Considera los Defectos del Proceso y la Reducción del Rendimiento.
◘ La Calidad en 100% implica que no hay partes que necesitan reprocesamientos.
Calcular ciertos índices de disponibilidad de una máquina no es tan complejo, ¿verdad?
¡Lo importante es comprender las necesidades de sus máquinas, para aplicar la estrategia correcta y mejorar el índice de disponibilidad en su empresa!